IMPACT BONDING – BOTTOM BONDING
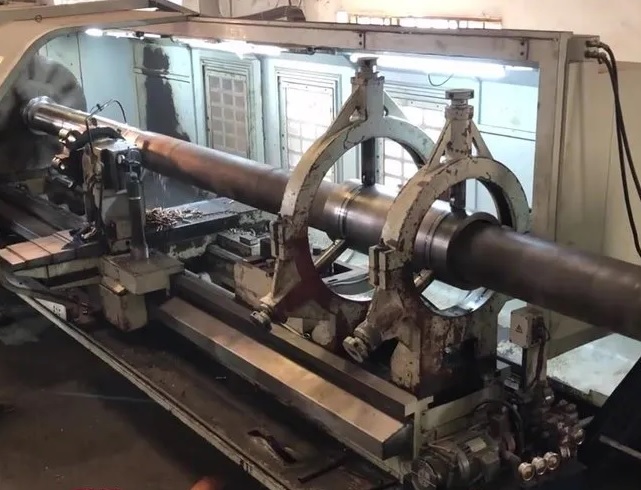
Bottom Bonding or Impact (Friction) Bonding is a heat-pressure technology that allows the spreading of an aluminium disc across the outer edge of a pan, protecting the otherwise exposed areas from direct heat and thereby significantly reducing the chance of “hot spots” occurring.
An impact bonding process is used to produce an encapsulated layer cooking vessel including a container structure having a bottom wall an intermediate layer and a cap structure The process includes centering the intermediate layer on the bottom of the container and welding the intermediate layer into place.
Welding the cap structure to the intermediate layer forms a resulting workpiece, The resulting workpiece is moved to a heating mechanism The resulting workpiece is heated to a temperature suitable for alloy or alloys used. The resulting workpiece is moved from the heating device and the resulting workpiece is loaded into a bonding die of a properly prepared impact press The impact press compresses the intermediate layer so that the intermediate layer is flattened and substantially fills a space between the bottom of the container structure and the cap structure , the intermediate filling layer being substantially encapsulated between the cap structure and the bottom of the container.